Safe Working Method Statement
Scope
This document has been prepared with a view to detailing and informing the customer in respect of the portable appliance tests undertaken by CG Electrical Equipment Testing. CG Electrical Equipment Testing performs these tests under the guidance of the Code of Practice for In-service Inspection and Testing of Electrical Equipment, which is a document produced by and available from The Institution of Engineering and Technology.
The equipment within the scope of this document includes electrical appliances for household and similar use, certain IT equipment supplied by plug and socket, luminaries and similar equipment. This document applies to all equipment fitted with the standard single phase 3 pin plugs. The tests performed only indicate the status of the safety of the equipment under test and although a functional test is performed, should not be misinterpreted as a verification of the unit’s compliance with operational specifications.
The Code of Practice defines equipment as: -
· Stationary Equipment or Appliances
· Information Technology Equipment
· Moveable or Transportable Equipment
· Portable Appliances
· Hand-held Appliances
· Fixed Equipment or Appliances
· Multi-way Adaptors and Extension Leads.
It must also be understood that some appliances (Class I) rely upon the fixed wiring of the socket to ensure continuity of the Earth connection. These tests ensure the appliance under test has the correct Earth connection resistance but cannot ensure the continuity within the fixed wiring of the supply and that a further examination of the circuits contained within the fabric of the building may be required.
The Law
The Code of Practice for In-service Inspection and Testing of Electrical Equipment, which was prepared by the Institution of Engineering and Technology with a view to determining the inspections and tests necessary to ensure that electrical equipment, is maintained properly to prevent danger. Although some references may be made to legislation within this document, the specific legislation should be consulted.
The legislation of specific relevance to electrical maintenance is as follows:
· The Health and Safety at Work Act 1974
· The Management of Health and Safety at Work Regulations 1999
· The Electricity at Work Regulations 1989
· The Workplace (Health, Safety and Welfare) Regulations 1992
· The Provision and Use of Work Equipment Regulations 1998
Initial Approach on Site
The CG Electrical Equipment Testing test engineer will, upon arrival on-site, make themselves known to the duty holder and/or client’s representative by reporting to main reception and explaining the works being carried out.
· The test engineer must park their vehicles legally and follow any traffic regulations or rules which may apply.
· The test engineer will sign the visitor’s book on arrival and must report to reception on departure.
· The test engineer will obtain a “permit to work” if appropriate.
· The duty holder or representative will be asked to accompany the test engineer around the site to highlight any sensitive areas that may affected by these works. They will also be asked to ascertain the schedule of testing and confirm any arrangements or appropriate times that have been made for shutting down any equipment.
· The test engineer must acquaint themselves with the Health and Safety Policy for the site.
· The test engineer must acquaint themselves with safety procedures relative to any potential hazards which may exist on the site and must adhere strictly to those procedures. Any specific areas are to be assessed for any risks.
· The duty holder or representative will be advised of any items that have failed and any additional concerns located within the premises. Previous inspection and test results should be provided to our engineer to assist in identifying any deterioration that may have occurred.
· Identity badges are to be worn whilst on site.
· All sub-contracting engineers are granted the appropriate authority when representing the company and can sign on behalf of CG Electrical Equipment Testing to finish the relevant documentation on completion of the services provided.
Permit to Work Documentation
If it is deemed necessary by the duty holder and/or client’s representative for the need of a “permit to work” certificate to be issued before any work is undertaken on the site, the test engineer shall ensure his compliance with the permit to work system as requested by the duty holder and/or client’s representative.
Permits to Work are a formal management system used to control high risk activities. These enable an assessment of risks to be made and to specify control measures which will be put in place to minimise the risk. If it is deemed necessary by the duty holder and/or client’s representative for the need of a “permit to work” certificate to be issued before any work is undertaken on the site, the test engineer shall ensure his compliance with the permit to work system as requested by the duty holder and/or client’s representative.
Personal Protective Equipment
Personal Protection is to be worn at all times where necessary,
· Safety Boots/Shoes
· Facemasks and Respirators*
· Safety Glasses or Goggles
· Safety Gloves
· Ear Defenders and/or Earplugs*
· Protective Headgear - Safety Helmets
· Hi-Viz Clothing
· Overalls and Protective Aprons*
*To be supplied by client if required to wear
General Protection and Safety
Protection required to client’s equipment and staff
Where possible work will be carried out so that there will be no risk to clients’ property. Where work is undertaken, and client site staff could potentially move through the work area a sign is to prominently placed warning of the potential danger to anyone who enters the area.
· Noise will be kept to a minimum but may be generated whilst working.
· Where spillage takes place when transporting rubbish from one area to another, this will be cleaned up.
· No temporary lighting is required
· No power supply is required
· No firefighting equipment is required
· Hand tools only required to carry out service
Definitions
As defined by the IET Code of Practice for In-service Inspection and Testing of Electrical Equipment
Basic Insulation
The definition refers to the insulation that is applied to live parts which is a fundamental aspect of most wiring and appliances to prevent electrical shocks. The breakdown of electrical insulation can be indicated by having equipment PAT tested, allowing organisations to act before the appliance in question becomes a danger.
Class I Equipment
These types of equipment do not just rely on basic insulation, but also have connections to a protective conductor for additional safety. The user is protected by a combination of basic insulation and the provision of an earth connection, thus providing two levels of protection. A large fault current flows from the mains part to earth via the protective earth conductor, which causes a protective device (usually a fuse) in the mains circuit to disconnect the equipment from the supply. There is no agreed symbol in use to indicate that equipment is Class I and it is not mandatory to state on the equipment itself that it is class I however the symbol may be used.
Class II Equipment
Class II equipment has either a reinforced insulation or is double insulated which provides the method of protection against electric shock. This means that as well as the basic insulation for live parts, there is a second layer of insulation, either to prevent contact with exposed conductive parts or to make sure that there can never be any contact between such parts and the live parts. The outer case of the equipment need not be made of insulating material; if protected by double insulation, a metal case will not present any danger. It must never be connected to earth, so connecting leads are two-core, having no protective conductor. The symbol for Class II equipment is two concentric squares illustrating double insulation as shown.
Class III Equipment
Class III equipment is defined as that in which protection against electric shock relies on that no voltages higher than safety extra low voltage (SELV) are present. SELV is described as a voltage not exceeding 25V ac or 60V dc. Such equipment is either battery operated or supplied by a SELV transformer.
Class 0 and 0I Equipment
Class 0 equipment features a single level of insulation which unfortunately means that one fault could cause an electric shock to its user or at the very least cause a spark that can easily escalate to a fire. Class 0 equipment is no longer acceptable in the UK as the protection against electric shock that relies upon basic insulation only.
Class 0I equipment is like Class 0 but has a power supply cord with no earthing conductor. The plug itself has no earthing contact They are often specialist equipment and should not be used without specific guidance on its use and the type of installation it is to be connected to. Such equipment is allowed only in very specific locations and should not be used in normal commercial, industrial or domestic environments.
Fixed Equipment or Appliances
A fixed appliance or fixed equipment is a piece of electrical equipment that is permanently wired into the electrical system in a specific location and permanently secured. They cannot be moved around like portable appliances as they often weigh 18kg or above, though some are lighter e.g. hand dryers and water boilers. Moveable or portable fixed equipment are connected to the electrical system via a fused connection unit (FCU) for security purposes. This practice is common in areas used by the public e.g. hotels, changing rooms etc.
110V Equipment NOT TESTED BY CG ELECTRICAL EQUIPMENT TESTING
110V Equipment (CTE – Centre Tapped Earth) has been encouraged in harsh environments such as construction sites or small residential refurbishments. The use of 110V equipment and other low voltage systems is mainly a UK based initiative but is not compulsory under law but has long been recognised as good practice. The use of 110V power tools reduces the risk of a fatality in the event of an accident and is signified by using yellow cables and connectors. The isolating transformers are used to provide two 55V lines out of phase which means that the connected tools, if a cable is accidently cut, the voltage is halved and the shock is less likely to prove fatal.
415V Equipment (Three Phase Equipment) NOT TESTED BY CG ELECTRICAL EQUIPMENT TESTING
415V Equipment, more commonly known as three phase equipment, is equipment fitted with a plug complying with BS EN 60309 and used for industrial purposes. Special tests leads are used to enable earth bond continuity and insulation resistance tests to be completed.
Inspection and Testing of Appliances
The preliminary inspection procedure is to first determine whether the equipment can be disconnected from the supply and disconnect if permission is received. If permission is not received to disconnect the supply no tests should be completed. It should be recorded that the equipment has not been inspected or tested and noted accordingly.
Preliminary or Visual Inspection
This test involves an in-depth check of the visual integrity of the plug, fuse, cable and case of the equipment under test. The electrical supply is required to be off for a complete visual inspection to take place.
The inspection will include the following: -
· the plug top is examined to ensure it is in physically good condition, is free from cracks or damage, any signs of overheating and that the pins are insulated. The top is removed to establish the outer sheath of the flexible cable is securely gripped by the cable clamp, to check conductor lengths and the terminals sufficiently tightened and is correctly wired.
· the fuse is examined to ensure it is of the correct rating for the type of appliance, it is manufactured to BS1362 and have an ASTA symbol displayed.
· the flexible cable is inspected for any signs of deterioration ensuring its length is suitable and safe for the equipment and the way it is used; it is in good condition and free from splits, fraying or damage.
· the appliance is inspected for any signs of deterioration or damage which might allow contact with live conductors. The casing or cabinet is inspected to ensure it is free from damage and/or cracks, that it switches on and off properly and is in good working order and operates safely.
· Assessment of whether the equipment is suitable for the environment.
Any minor faults that are identified during the visual inspection, for example: damaged plugs, incorrectly rated fuses and loose connections will be rectified prior to the testing procedure.
In addition to the preliminary inspection some or all of the following tests are completed which are subject to the Class of the appliance.
· earth continuity test
· insulation resistance test
· protective conductor current
· touch current test
· substitute/alternative leakage test
· functional operation
Earth Continuity Testing
This test can only be applied to Class I equipment or lead cord sets. This test ensures that an earth connection is made between the exposed metalwork of the appliance and the earth pin of the plug top. Earth continuity tests made on computer equipment are “soft tests” of 100mA and no functional test is carried out on the personal computer central processing unit.
Insulation Resistance Testing
This test is performed between live conductors, i.e. phase and neutral, connected together and the body of the appliance. A test voltage of 500V dc is applied and the Insulation Resistance determined to ensure adequate protection is in place between the conductors. Sometimes when a test is completed at 500V dc, the voltage being used can trigger a false reading or the surge protection circuit. In this instance an alternative insulation test of 250V dc will be used as this will not trigger the surge protection within the appliance.
Earth Leakage or Protective Conductor Testing
An Earth Leakage or Protective Conductor test is an alternative or complementary test to the insulation test and is carried out on Class I appliances. The test is completed to measure the amount of current leakage and is measured from the internal live parts to Earth. The test will establish the level of this leakage and if this level is low enough to cause no harm to the user of the appliance. No insulation is perfect and there is always an amount of leakage even if this is nominal.
It can be used as an alternative to the insulation resistance test when the insulation test can’t be performed. When carrying out this test and using rotating machinery such as drills and grinding machines, always secure the appliance so that when the power is applied the appliance will not cause injury, once the equipment has been switched on and operating for a short period of time, the measurement is made and recorded.
Touch Current Test or Measurement
A Touch Current test is for Class II appliances and is carried out as Class II appliances do not have an earth. There are two different methods of testing that can be used, one is a probe test where an earth bond lead is used as a probe to measure any current leaking onto the enclosure or casing. The other method is to use a differential test where the test meter will measure the amount of current being supplied to the appliance and how much current is being returned before calculating the difference.
Polarity Check
A polarity check is performed to check to ensure that the live and neutral conductors are not crossed. This can only be done if access can be gained to both sides of a power cord.
Multi-way Adaptors and Extension Leads
Sufficient socket outlets should be provided so that multi-way adaptors and extension leads are not necessary. Inspection of the installation should decide what is reasonable in terms of safety and a report made to the duty holder if excessive numbers are being used. They should not be connected in series i.e. daisy-chained.
Residual Current Device, Adaptors and Extension Leads
Residual Current Device or RCD adaptors and RCD extension leads are used to provide protection for persons using portable appliances particularly equipment outdoors. RCD Adaptors continuously monitors the power supply to an electrical appliance and cuts off the power within 40 milliseconds if an earth current fault is detected. This is fast enough to prevent a fatal electrical shock. Electrical appliances can become dangerous if the wiring becomes loose, if they or their power cords become damaged or if they get wet.
Point to Point Testing of Fixed Equipment or Appliances
Point to Point testing of fixed equipment or appliances is more difficult to inspect and test because of the nature of their attachment to the building fabric and their connection to the fixed wiring of an installation, usually via an isolator or fused connection unit (FCU). This doesn’t mean that only visual inspections are required for these types of equipment, they should still receive a full combined inspection and test at relevant intervals. These intervals or frequency of inspections and test should be determined by a risk assessment.
Fixed equipment testing can be undertaken during the Electrical Inspection Condition Report. (formerly known as a Periodic Inspection report) of the fixed installation where the frequencies of any inspection and testing are like those for the fixed installation. Additional formal inspections may be required for equipment that could be subjected to higher use or have a greater potential for being damaged, e.g. hand dryers, fixed hairdryers etc.
Testing fixed equipment or appliances must be carried out by a competent person, in accordance with the specific tests for the Class of equipment. The person carrying out the inspection and testing: -
· must be competent to carry out safe isolation procedures
· must be competent to carry out this more complex arrangement of work
· must ensure safe systems of work are observed always
· must ensure all inspections and tests, are relevant to the class of equipment
Fixed appliances which have been designed to be secured in a specific location may require the isolation of the supply which must be agreed by the duty holder at the time of inspection. This testing will be subjected to the relevant Safe Isolation procedures however any limitations, which may have been imposed during the inspection and testing of the appliance, will be noted i.e. unable to isolate supply due to operational requirements.
Marking and Recording Results
Every appliance on passing the required standard to indicate that it is in a safe condition will have a non-destruct appliance label attached to a suitable part of the equipment stating unique number, date of test and initials of testing engineer.
A record generated within an inventory/testing report stating:
Unique number (as noted on appliance label)
Appliance description
Date of test
Test engineer
Test results
Testing appliance, serial number and calibration date
Any relevant comments
Documentation
Upon completion of the testing electronic copies of the test reports shall be generated and forwarded to the duty holder who is responsible for the ongoing maintenance of the appliances. These reports will detail the appliances, their location at the time of testing, the results and any repairs completed.
Appliances that FAIL the testing procedure will be listed and highlighted with any course of action required. In addition to the report, a certificate shall be provided for display on the premises to advise that all electrical appliances have been tested for electrical safety.
Failed Items
Those appliances found to be damaged or faulty and FAILING the inspection will be removed from service and marked with a FAILED label stating that the appliance is not to be used. The owner at the position of the failed item will be informed immediately and at the end of the day, the duty holder or responsible person will be advised of all failures, the reason for failure. The course of action will be decided by the responsible person or duty holder. At any point if the appliance can be repaired CG Electrical Equipment Testing will do so to reduce downtime.
Microwave Ovens
Microwave ovens provide a convenient and safe way of cooking food in the workplace; however, faults can occur and unless periodically tested they may become a health and safety hazard without you being aware. Additional Requirements for Microwave Ovens are covered by the BS EN 60335-2-25 Safety Standard. CG Electrical Equipment Testing will perform additional tests to ensure the appliance under test is working optimally, due to these extra tests there may be an additional fee charged.
Microwave Power
This involves heating a known volume of water for a known period and calculating the power generated by the oven as a function of the period and difference in temperature generated in the water.
Microwave Leakage
Lack of cleanliness and poor maintenance of the door seals can lead to leakage levels that exceed the recommended limit. Testing of the unit involves measurement of the radiation levels around the oven using microwave detection instrument to ensure compliance with the 5mW/cm2 limit.
Door Interlock
The safety interlock switches and the door seals are inspected for any signs of damage to ensure that they function correctly and safety.
Risk Assessment and Hazard Identification
An assessment of risk is nothing more than a careful examination of what could cause harm to staff, so that you can weigh up whether you have taken enough precautions or should do more to prevent harm. The aim is to make sure that no one gets hurt or becomes ill. Accidents and ill health can ruin lives and impede the effective operation of the company.
Specific hazards in the testing environment shall be discussed with the duty holder at the time of site survey.
The risk rating for individual hazards can then be classified as follows:
The higher the score, the higher the risk and the higher the hazard priority for control measures
Individual Risk Rating
1 – 4 LOW This is the usual rating you would expect and in the majority of cases is the normal condition using the correct control measures, but an accident or incident could still happen.
This is the ideal and every effort must be made to reduce and maintain the risk rating within this band.
5 – 10 MED Record the findings of your assessment and introduce additional control measures to improve the Risk Rating.
Certain activities will be out of your control, so every effort should be exercised when carrying out such activities with medium risk
11 – 25 HIGH Stop immediately/do not start activity and seek further advice
NOTE: If any individual hazard has a rating of 8 or higher and/or the total hazard rating is 25 or above a more in-depth assessment is required.
Reliable appliance testing across South Wales.
© 2025. All rights reserved.
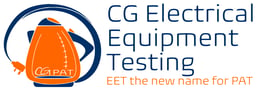
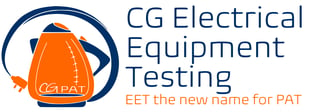